|
When you start lifting your rig like this, you WILL encounter driveline problems. High Angle Driveline has the solution. Both trucks are customers of High Angle Driveline. |
So what causes a driveshaft to do this? The main problem is the operating angle of the shaft. Ideally you want the two ends of a drive shaft to be within a few degrees of each other for maximum u-joint life and minimum vibration. If the angles aren’t correct, you will experience vibration. Anytime you add a lift, you risk the chance of the angles be out of wack. Larger lifts are worse of coarse. The more angle you have on a shaft, the more likely you will have this problem. This also decreases your u-joint life. Basically a u-joint is rated for specific, continuous operating load @ 3000 R.P.M. for 5000 hrs. with a 3 degree joint angle, and assuming proper periodic maintenance. If you double the angle you halve the life, halve the load & double the life and vice/versa.
|
When a
vehicle is lifted, this affects the driveshaft angle. Notice the
driveshaft angle can not exceed 3 degrees from each centerline.
Both t-case and axle angles have to match each
other. |
Besides vibration problems we also had problems with the front shaft. Apparently with the soft front springs, longer shocks, mounts and removed sway bar, it must have been too much for the front shaft. The 1310 CV came apart twice on the trail. The front shaft just didn’t have enough travel.
It was time to find some new shafts. We wanted something that could handle the flex of our rig. We recently did 986 RTI on a 25 degree ramp so we needed shafts that could extend farther and not bind at an extreme angle. Another thing we considered was the output of our motor. We’ve seen other driveshafts that had either been snapped like a toothpick or twisted like candy cane from too much torque and hp. Granted our big block engine is still mostly stock but we have some major engine mods coming soon so we wanted something that could handle the power.
Here's the
rear 1350 CV shaft almost ready to leave the shop. Jesse does the
final checks to make sure everything is correct. Here's the
operating angle on the shaft. Over 32 degrees which is remarkable
for any shaft. Our old shaft could only operate at 23
degrees.
Click picture for larger
image
|
Luckily for us, Jesse Jaynes for High Angle Driveline came to our rescue. High Angle builds custom shafts and components for extreme duty and long travel 4x4 applications which include all 4x4s, Jeeps, trucks, racing and More. High Angle Driveline uses only the best parts, including genuine Dana & Spicer components. All driveshafts are precision fabricated and balanced professionally. Jesse suggested his custom 1350 CV style shafts front and rear. To start with, the 1350 u-joint is designed for a 1 ton truck so there should be no strength issues there. The 1 ton joints are then added to a a CV style shaft. High Angle Driveline is the only shop we know that can produce a 1350 CV that will bolt to our 205 t-case.
|
Here's the
benefit of a CV shaft. Notice the t-case doesn't have to be angled
making it easier for the front shaft. The rear axle can be pointed
up to the t-case with no problems. A standard shaft can't do
this. |
The real benefit to a C. V. (double cardan) drive shaft is smoother operation at higher operating angles and longer life. The C.V. assembly works by intersecting the joint angles at the center pivot point and delivering a smooth rotational power flow or surface velocity through the drive line. Therefore, with this type of driveline it is important to roll the differential upward so that you have minimal joint operating angle at the differential end. Rolling the differential upward will lessen the total operating angle at each end of the driveshaft. Now at the transfer case end of the driveshaft you have two joints equally dividing the total angle. This will double the life of the joints at this end, additionally you will be back up to full rated life for the joint at the differential end. As another benefit, the C.V. is it’s stronger than a conventional driveline when turning through the same angle.
The rear 1350 CV shaft requires a fixed yoke 205 which shouldn’t be a problem since almost all 205’s have this. Unfortunately for us, our NP205 does not have a fixed yoke. 1980 was the only year GM had a slip yoke on the end of a 205 transfer case. Well, guess which year our 205 was made… Fortunately, we found a used 205 for $200 that had the fixed yoke on it. We could of purchased new parts but it was almost the same cost. This will also allow us to install the slip yoke on the other transfer case and sell it. All the fixed yoke parts are installed except for the yoke. The new CV shaft can now be installed.
At the same
time, we converted our 205 into a fixed yoke. 1980 was the only
year that the 205 came with a slip yoke and we just happen to have
a 1980... Lucky us. Right picture shows the new flange
installed.
Click picture for larger
image
|
To install the new CV shaft in the rear, Jesse includes a special custom flange that bolts on to the existing shaft in place of the fixed yoke. The flange is easy to install and requires not special tools. A large socket is required to remove the large nut holding the yoke on. Jesse also includes special high strength bolts to mount the shaft on the flange. The shaft is bolted to the custom flange and installed on the axle. This is a good time to replace the joint straps or u-bolts.
For the front shaft, Jesse built a custom rock crawler shaft which allows major flex without the shaft falling in pieces. This shaft has a longer slip shaft which is needed more in the front that the rear. It’s also equipped with the 1 ton 1350 shafts on both sides and also includes the 1 ton CV joint. This shaft does require a few things. The front flange has to be sent to High Angle Driveline so Jesse can machine it to fit the larger CV. It also requires a 1350 yoke on the front axle. After the flange is machined, it’s installed followed by the driveshaft. New u-bolts is required for our new axle yoke which were supplied by High Angle.
Now that we’re shafted, it’s time for a test spin. Let’s just say this wasn’t an ordinary spin. We really took it for a test by dropping the clutch at 5k and proceeded to take it on the highway at high speeds. 90mph and no vibration! We were Lucky the police weren’t following us! No annoying chattering noise either. This was so nice and everything was so smooth. We even locked in the hubs and shifted it in 4 HI and tried the front shaft. Again, no vibration at higher speeds. We now have one smooth rig!
![]() Paradise, CA 95969 (530)872-5725 ![]() E-Mail: forwhlr@saber.net www.highangledriveline.prodigybiz.com |
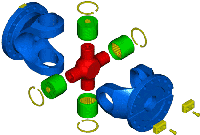
chevy@off-road.com
Back to Project Potent Rodent Back to the Chevy WebPages