78-79 Bronco A/C Compressor Conversions
A how-to article for converting your Big Bronco's
air conditioner into an on-board air compressor.
By Erik Marquez
In order to build a AC/Air compressor you must follow three simple principles:
1. You must have a need (or at least the need to point and say "hey guys look what I built this weekend"2. You must have more time than money.
3. It helps if you have most of the parts required sitting in your shop somewhere collecting dust.
The basic parts of the system are a stock type AC
compressor with brackets, an air holding tank of some sort,
pressure switch, relief valve and a on/off switch.
This is Erik's extremely clean
compressor installation.
Note that all wires are protected
by convoluted sleeves.
If you need to get a compressor, or want to find
out what size your York is there are a few ways to check. The
sure fire method is to remove the clutch assembly, and look at the
output shaft. There are three basic models of the York full size
compressor.
The compressor it self can be mounted in a number of ways. If you currently do not run AC than the easiest and most reliable way is to use stock brackets, this is what I did. Most AC compressors are full of oil in the system for lubrication. Some compressors do not have an oil sump, and the oil charge is mixed in with the refrigerant. Luckily the York pump is not this way. It has a oil sump separate from the compressor side. It does however still allow some small amount of oil to the front seal, and into the discharge side of the system. The York pump should be mounted with the discharge side up to minimize oil discharge. You can also modify your pumps oiling passage to the front seal. I have done this on both of my pumps. I see less oil in the separator, and no reliability problems so far. The procedure for modifying the oil passage is very simple. In order to plug this oil passage, you need to remove the front seal from the compressor.
Remove the pulley and the magnetic clutch coil. Then remove the 6 - 1/4 inch hex head screws from the seal retainer, remove the retainer and seal. Check the compressor manual if you are not familiar with these operations. The manual can be downloaded from this site: York compressor service manuals
The oil hole is 5/32 inch in diameter. The pump shown in the picture is a Right side suction model. If you have a Left side suction model, the hole will be on the left. Cover the bearing with several layers of towels. Plug the hole with a wad of paper towel shoved about 1 inch into the hole to keep metal chips out of the suction port. Drill and tap with a 10-32 thread tap. You are supposed to use a #21 drill with the 10-32 tap, but the 5/32 hole is so close that you don't really need to drill it out. I used a shop vac during the tapping to minimize any chances of metal getting where it did not belong. Carefully vacuum out any remaining metal chips and cover the outlet port and blow compressed air into the inlet port to blow the paper towel plug out of the oiling hole along with any chips. Brush out any remaining chips and then remove the towels. Put a drop of blue locktite on a 10-32 x 3/8 set screw and tighten it into the threaded hole. Reassemble the seal, seal retainer, clutch and pulley and you are done. Once this modification is done, you will still some small amount of oil in the discharge side of the compressor. Oil in the air line for our use is not such a good thing. One way address the problem is to use an oil/water separator in the air line between the pump and the tank. This is what I've done and it seems to work for me. As extra insurance I use a disposable paint gun type filter attached to my tire valve air chuck. That way I know no oil gets into my tires.
Next decide what to use as an air tank and decide where to mount it. While you can use a old fire extinguisher like I did, I would not recommend it. It complicates plumbing, because of a lack of inlet/outlet ports, necessitating rethread of the only port to NPT and in general probably is not as safe as a prefab tank. Since building my system I have found air tanks of suitable size for as little as $68.00 and I'll be changing mine real soon. As for mounting the tank I built a flat plate with stainless steel hose clamps as tank brackets and then bolted the plate to the left fender well. The pressure switch controls when the compressor activates and stops. I chose an adjustable one. It kicks in at 100psi and shuts off at 145psi. This is a standard 110V air compressor unit. Available for under $12. A on off switch in my dash panel controls the power to the compressor clutch and a solenoid I use to bump up the idle when ever the compressor is activated. I also have a hand throttle to control the engine speed if I want more RPM's than the solenoid will provide.
For safety you need to add a pressure relief valve rated to release at a pressure lower than whatever your tank can safely hold. Keep in mind that AC compressors have a tremendous high pressure capability. To keep the intake air source clean you'll need to provide some sort of filter. My system uses a small K & N air filter mounted directly to the low side port. Again opinions vary, but this seems to work for me.
Lastly you'll need to plumb the whole mess. I strongly recommend a custom made high pressure, high heat line be made for the discharge side to tank connection. You can have them made to your specs at any NAPA, Diesel truck service center or hose supplier for about $15.00. I went through three "home made" supply lines before I went the custom route. The remainder of the lines and connections can be done with standard 3/8 air line and brass fittings. This is an area where you can do it cheaply (brass fittings/air line) or go hog wild and have custom lines made for every thing.
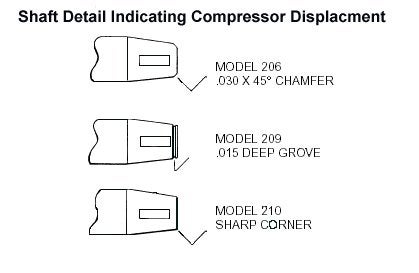
Model # Cubic in per rotation How to decode
F206R |
6 Cubic inch per rotation |
First digit is type of hose fittings F=Top Flange R=Roto lock T=tube-O 2nd digit=number of cylinders 3rd & 4th digit=cu in. displacement of air during one rotation 5th digit= R=right hand L=left hand |
F210R |
10 Cubic inch per rotation |
|
R209R |
9 Cubic inch per rotation |
|
R210L |
10 Cubic inch per rotation |
The compressor it self can be mounted in a number of ways. If you currently do not run AC than the easiest and most reliable way is to use stock brackets, this is what I did. Most AC compressors are full of oil in the system for lubrication. Some compressors do not have an oil sump, and the oil charge is mixed in with the refrigerant. Luckily the York pump is not this way. It has a oil sump separate from the compressor side. It does however still allow some small amount of oil to the front seal, and into the discharge side of the system. The York pump should be mounted with the discharge side up to minimize oil discharge. You can also modify your pumps oiling passage to the front seal. I have done this on both of my pumps. I see less oil in the separator, and no reliability problems so far. The procedure for modifying the oil passage is very simple. In order to plug this oil passage, you need to remove the front seal from the compressor.
Remove the pulley and the magnetic clutch coil. Then remove the 6 - 1/4 inch hex head screws from the seal retainer, remove the retainer and seal. Check the compressor manual if you are not familiar with these operations. The manual can be downloaded from this site: York compressor service manuals


The oil hole is 5/32 inch in diameter. The pump shown in the picture is a Right side suction model. If you have a Left side suction model, the hole will be on the left. Cover the bearing with several layers of towels. Plug the hole with a wad of paper towel shoved about 1 inch into the hole to keep metal chips out of the suction port. Drill and tap with a 10-32 thread tap. You are supposed to use a #21 drill with the 10-32 tap, but the 5/32 hole is so close that you don't really need to drill it out. I used a shop vac during the tapping to minimize any chances of metal getting where it did not belong. Carefully vacuum out any remaining metal chips and cover the outlet port and blow compressed air into the inlet port to blow the paper towel plug out of the oiling hole along with any chips. Brush out any remaining chips and then remove the towels. Put a drop of blue locktite on a 10-32 x 3/8 set screw and tighten it into the threaded hole. Reassemble the seal, seal retainer, clutch and pulley and you are done. Once this modification is done, you will still some small amount of oil in the discharge side of the compressor. Oil in the air line for our use is not such a good thing. One way address the problem is to use an oil/water separator in the air line between the pump and the tank. This is what I've done and it seems to work for me. As extra insurance I use a disposable paint gun type filter attached to my tire valve air chuck. That way I know no oil gets into my tires.
An old fire extinguisher
can be used as an air tank,
but a tank meant for the job would
be easier and safer.
Next decide what to use as an air tank and decide where to mount it. While you can use a old fire extinguisher like I did, I would not recommend it. It complicates plumbing, because of a lack of inlet/outlet ports, necessitating rethread of the only port to NPT and in general probably is not as safe as a prefab tank. Since building my system I have found air tanks of suitable size for as little as $68.00 and I'll be changing mine real soon. As for mounting the tank I built a flat plate with stainless steel hose clamps as tank brackets and then bolted the plate to the left fender well. The pressure switch controls when the compressor activates and stops. I chose an adjustable one. It kicks in at 100psi and shuts off at 145psi. This is a standard 110V air compressor unit. Available for under $12. A on off switch in my dash panel controls the power to the compressor clutch and a solenoid I use to bump up the idle when ever the compressor is activated. I also have a hand throttle to control the engine speed if I want more RPM's than the solenoid will provide.
The small solenoid keeps the idle
speed up when the compressor clutch is engaged.
For safety you need to add a pressure relief valve rated to release at a pressure lower than whatever your tank can safely hold. Keep in mind that AC compressors have a tremendous high pressure capability. To keep the intake air source clean you'll need to provide some sort of filter. My system uses a small K & N air filter mounted directly to the low side port. Again opinions vary, but this seems to work for me.
A small K&N Filter keeps the
intake air clean.
Lastly you'll need to plumb the whole mess. I strongly recommend a custom made high pressure, high heat line be made for the discharge side to tank connection. You can have them made to your specs at any NAPA, Diesel truck service center or hose supplier for about $15.00. I went through three "home made" supply lines before I went the custom route. The remainder of the lines and connections can be done with standard 3/8 air line and brass fittings. This is an area where you can do it cheaply (brass fittings/air line) or go hog wild and have custom lines made for every thing.
|
Follow @Off-Road